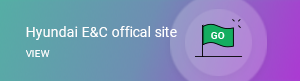
Hyundai E&C doubles effort to secure a free-form manufacturing technology and future construction technologies by developing a technology utilizing 3d-printed large composite materials.
Securing Free-Form Mold Manufacturing Technology by 3D Printing Large Composite Materials
With a goal to develop a 3d printing technology in the field of free-form architecture, Hyundai E&C has collaborated with a 3d printing specialized company, 3D Factory, to study 3d printable composite materials and has successfully secured a technology of manufacturing a free-form mold whose patent is currently being filed.
A wide-range of materials can be used for 3d printing. It can range from low-strength plastic to high-strength carbon fiber and glass fiber, and it is possible to mix 2 or more different materials to create a completely new material with optimum performance.
The disadvantages of conventional materials used for mold forms such as plywood or steel were the difficulty of realizing unstructured free-forms, with higher manufacturing costs and production period. However, Hyundai E&C’s latest developed technology of manufacturing free-form mold form applying 3d printed composite materials uses a large industrial-grade 3d printer capable of printing and surface processing, enabling a precision tolerance of maximum 0.001 mm. It allows for an one-step manufacturing of a 2.5cmx5cmx1.5cm sized mold which helps to drastically reduce manufacturing lead time and secure cost-effectiveness and high quality.
[Free-Form Mold Manufactured with 3D Printing Technology]
Recently, Hyundai E&C has been studying how to apply the 3d printing technology to molds that are used to manufacture lining which forms the inner wall of a tunnel after excavating the ground with the TBM(Tunnel Boring Machine) machine, which the sophisticated mechanical tunnel boring construction method. The company manufactured and assembled free-form fillers that will go into the steel mold form by 3d printing composite materials to effectively manufacture different forms of curved segments, ultimately improving quality and drastically reducing manufacturing costs.
[Application of 3d Printed Fillers Inside the TBM Segment Mold Form]
Developing and Commercializing Technology of Manufacturing 3D Printed Free-Form Bench
Hyundai E&C has developed the technology of manufacturing a free-form landscape structure by 3d printing of composite materials and filed for the relevant patent last July (patent no. 10-2020-0090790, method of manufacturing a free-form landscape sculpture using 3d printing technology and free-form bench manufactured thereof).
The 3d printing technology involves additively manufacturing a three-dimensional model, with excellent free-form manufacturing ability, enabling precision construction and free variations of colors and materials in realizing diverse designs. However, due to limitations of 3d printable materials and equipment, there are only cases of commercializing large-scale 3d printing technology in the construction sector.
Korea’s first free-form landscape architecture, manufactured by Hyundai E&C, is a 1mx1mx8m outdoor bench, which was additively manufactured and processed by 3d printing 200 components. Hyundai E&C used noninflammable eco-materials to ensure its safety and certified by the industrial good quality scheme Q Mark for its outstanding quality.
[Korea’s First Free-Form Bench Applying 3D Printed Composite Materials (Hill State Lake Songdo-2)]
Starting with Hill State Lake Songdo-2 whose residents all moved in last year, Hyundai E&C plans to further apply the above technology to landscape architectural structures of its THE H site. An official from the company’s R&D center said that “by developing the technology of 3d printing large composite materials, Hyundai E&C will further develop the construction technology based on 3d printing of construction materials, thereby driving the paradigm shift in the future construction sector.”