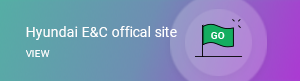
The movie Concrete Utopia tells the story of the residents of the only apartment in Seoul that remained intact following a devastating earthquake. The "concrete" in the title is a metaphor for “apartment” because it takes a lot of concrete to build an apartment. According to one study, it takes 185 tons of concrete to build one apartment building with a floor area of 84㎡. This probably explains why the film uses concrete instead of the word "apartment" in the title.
The main construction material for roads, tunnels, and other infrastructure we encounter everyday including in our homes, is concrete. It’s no exaggeration to say that concrete is everywhere we go. It’s the second most consumed material on Earth after water, but how long has it really been with us?
The Two Thousand Year Legacy of Concrete
Concrete comes from the Latin word “concretus”, which means “growing together”, and the idea of "growing" makes us think of tall buildings. No one knows exactly where concrete was first used or who invented it, but it’s believed to have been used in ancient Egypt and Rome.
Traces of concrete, a mixture of lime, volcanic ash, and seawater, can be seen in the Colosseum, Pantheon, and other buildings built by the Romans over 2,000 years ago. How these structures have survived to this day is a testament to the durability of the material.
[ The Colosseum and Pantheon in Rome, both made of concrete. They are preserved as tourist attractions that offer a glimpse into excellent ancient architectural engineering ]
People often confuse concrete with cement, and although they are not entirely incorrect, there is a big difference between the two. Cement is the name of an material, while concrete is a mixture of cement and other aggregates, such as water, sand, and gravel, that are then formulated and hardened. Take flour dough as an example. The main ingredient, flour, is the cement, and the dough mixed with water and other ingredients is the concrete.
The resulting mixture of cement, water, and sand is called mortar. Mortar is used to adhere things like tiles and bricks, and when aggregates like gravel are added to the mortar, it becomes concrete. On a construction site, concrete is sometimes referred to as ready-mixed concrete, which means it's not quite hardened so it can be transported to the site and then poured right away.
Concrete, The Longtime Irreplaceable
Concrete's performance depends on how it’s prepared. Just as flour can be made into any shape you want when it’s a dough, but once it’s heated and hardened, it's hard to reshape it. The same goes for concrete. The great thing about concrete is that it's flexible enough to be molded into many different shapes when it’s soft, and when it hardens, it becomes very stiff, making it more durable for buildings. Concrete strength is measured in units called MPa (megapascals). For example,1 MPa can withstand a load of 100 tons per 1m².
Concrete is used in many construction sites because of its low price and low maintenance costs. Of course, there are disadvantages such as a long construction period and the influence of weather during the curing process, but no other material can match concrete in terms of durability, which is the most important factor for any building. With the progress of industrialization, structures have become larger and taller, and they have gradually acquired additional qualities such as high strength and durability. Recently, there have been various attempts to improve constructability and reduce carbon emissions by integrating all kinds of new technologies.
35 Years of Research at Hyundai E&C, Beginning with a Group of Concrete Experts
Hyundai E&C has been actively responding to the changing construction environment since 1990, being the first builder to organize a group of concrete specialists. This is a decade in advance of other construction companies. Our research spans the entire process, from material source technology to manufacturing, construction, and curing (protecting the exposed surface of concrete).
In the early stages of our research, Hyundai E&C focused on developing technologies to increase the concrete's strength, which is the most important aspect of concrete. The company started developing concrete with a compressive strength of more than 40 MPa, which is used in apartment buildings, and was successfully introduced 100 MPa concrete in 1992.
Around 2005, research on high-strength concrete was so intense that those days were called the "era of high-strength concrete." In 2007, Hyundai E&C gained a competitive advantage by developing the highest strength concrete in Korea (200 MPa), exceeding the level of 150 MPa developed at the time.
Continuing its efforts to improve quality, in 2015, Hyundai E&C introduced the "Vertical Pipe Cooling Method" for the first time in Korea, which is effective in controlling temperature cracks in concrete with elongated and thick shapes such as walls, while the "Automated Concrete Curing Method," recognized as the New Construction Technology (No. 760), was applied to the Dangjin Nuclear Power Plant Units 9 and 10 and the Tuas Finger 1 landfill project in Singapore, resulting in a dramatic reduction in cracking and curing periods.
Whether a technology would succeed or not is determined when it’s applied to real-world projects, and Hyundai E&C's technological prowess is especially significant because it has actively applied it to a wide range of sites both at home and abroad. Not only apartment complexes, but also large facilities such as bridges and power plants, and in 2010, Hyundai E&C developed and successfully deployed the optimal locally customized concrete for the construction of a nuclear power plant in the United Arab Emirates (UAE), one of the largest overseas sites.
The company has steadily carried out researches to lower carbon emissions since the 1990s. As a result, in 2015 and 2020, we developed "Green PHC Pile" and "Non-cement Solidifying Agent" that helped reduce carbon emissions and were received green technology certification for these achievements. We also introduced high-performance concrete to solve the problem of inter-floor noise in apartments. In 2022, Hyundai E&C developed "High Density Specialized Mortar" with slag aggregate, which weighs more than ordinary sand, and contributed to obtaining Korea's first Class 1 inter-floor noise reduction technology recognized by the Korea Land and Housing Corporation (LH).
In addition, we recently developed an "early strength concrete" technology that can secure high compressive strength in a shorter time compared to ordinary concrete, and became the first Korean firm to acquire the Ministry of the Interior and Safety's designated disaster safety new technology (No. 2023-27) in the field of concrete.
Weatherproof Concrete Technology for Optimal Construction Sites
Here's a closer look at some of the top technologies that Hyundai E&C's concrete experts have selected to improve quality, enhance performance, make concrete more functional, and lower carbon emissions.
- "Vertical Pipe Cooling" and "Automated Curing Method" Improve Quality with Temperature Crack Control
One of the key aspects of concrete quality is managing the hydration heat (the heat generated when cement and water chemically react). This is because high heat of hydration results in higher temperatures at the center and lower temperatures toward the surface, and the temperature difference between the center and surface can cause cracks to form. Structures on large sites in particular use bulky mass concrete. The larger the mass, the more difficult it’s to control temperature-induced cracking, so reducing the hydration heat is key. Hyundai E&C has developed "Vertical Pipe Cooling" that can be applied to large, vertically long concrete structures such as retaining walls, bridges, and pylons, and "Automated Curing Method" optimized for mass concrete structures to control temperature-induced cracks.
The Vertical Pipe Cooling method is a technology that reduces the hydration heat by installing pipes vertically in the structure and injecting cooling water to reduce the heat of hydration, thereby controlling temperature cracking. This method can help reduce concrete temperature cracking by more than 70%. In addition to acquiring two related patents in Korea, Hyundai E&C also received a technology award from the Korean Concrete Institute.
Recognized as a new construction technology, the Automated Curing Method installs temperature sensors at the center and surface of the structure to pour concrete, and automatically supplies hot water to prevent cracks in the concrete when there is a temperature difference. This technology can not only control temperature cracks but also cracks caused by drying shrinkage, and it’s also highly effective in saving manpower due to automation.
- Ultra-high Strength, Ultra-Performance Concrete Technology
Apartments typically use concrete with a strength of 20 to 40 MPa, while skyscrapers and bridges bearing heavy traffic require higher strength and thicker concrete at the lower part of the structure to withstand the weight of the top. While ordinary concrete combines reinforcing bars and expands its cross-section to compensate for tensile force (the force that stretches or pulls an object), ultra-high-performance concrete can be mixed with steel fibers and fine particles to increase its tensile force and strength. This can reduce the weight of the building itself as well as the area of columns or wall structures, allowing for a larger interior space. In 2007, Hyundai E&C became the first company in Korea to introduce 200 MPa ultra-high-performance concrete technology, which is 10 times stronger than ordinary concrete. This is the strength sufficient enough to construct buildings up to 270 stories using only reinforced concrete structures. In addition, Hyundai E&C has commercialized 80 MPa concrete technology and has successfully deployed it to the Godeok Bridge (80 MPa), Busan Eco Delta City Bridge 8 (150 MPa), and Lusail Tower (80 MPa) site in Qatar.
- Hollow Glass Power, New Material for Functional Concrete
Hyundai E&C is also making diversified attempts to become more competitive. In 2022, in a bid to overcome the challenges of high-strength concrete construction, Hyundai E&C successfully applied a new material called Hollow Glass Powder to concrete for the first time in the world. To produce high-strength concrete, more cement is used, which makes the dough more sticky. In this case, adding a little hollow glass powder (rounded shape) like a food seasoning, helps to reduce the viscosity, making it much easier to transport with a pump and revet with a vibrator. Currently, it has been applied to Hillstate Byeolnae Stay One and Hillstate Ijin Bay City, and will be expanded to sites that require high-strength concrete, mainly high-rise buildings and super-long bridges.
- H-ment and Green PHC Pile, New Materials Reduce Carbon Footprint
Concrete is made by mixing cement and aggregate, which emits a lot of carbon dioxide during the production process. Therefore, Hyundai E&C began to research how to reduce carbon emissions by reducing the amount of cement used. This led to the development of H-ment, a material that utilizes cement substitutes. By using the product generated in the process of making pig iron in steel mills to make concrete instead of cement, carbon emissions can be reduced by up to 35%. In addition, as a pre-mixed product that is modified in advance, it’s able to maintain uniform quality, dispelling concerns about reduced strength.
In addition, Hyundai E&C has reduced carbon emissions by utilizing slag in concrete piles, which sturdily support structures, hence the name Green PHC (Pretensioned spun High strength Concrete) piles. While maintaining the performance of conventional PHC piles, it has received a green technology (GT-15-00090) distinction from the Ministry of Land, Infrastructure, and Transport for its superior carbon carbon-lowering results such as using 40% fine slag powder instead of cement.
- Korea's First Early Strength Concrete to Receive New Disaster Safety Technology Distinction
Recently, Hyundai E&C received the Ministry of the Interior and Safety's New Technology for Disaster Safety (No. 2023-27) distinction for its early strength concrete, which hardens quickly with higher compressive strength than ordinary concrete. This is the first time in Korea that a concrete technology has been certified as a disaster safety new technology. This technology is particularly competitive in winter construction. Unlike ordinary concrete, which needs to create an environment of 10℃ or higher by supplying heat energy with lignite, heaters, etc. during curing, Hyundai E&C's technology accelerates the cement hydration reaction when meeting the temperature condition of 5℃ and achieves a strength of more than 5MPa within 24 hours, which not only saves construction time and reduces heating costs, but also minimizes safety hazards such as gas leakage, asphyxiation, and fire. This technology, incorporating Hyundai E&C's construction time saving technology, has been deployed to Jemulpo undergrounding site, the Daegok-Sosa double-track subway site, and will be implemented at the Yeongdong-daero underground space complex development site in the future.
- “QCON”, Concrete Quality Prevention System Utilizing Big Data
In addition to securing the source technology, Hyundai E&C has also introduced a system to effectively manage concrete quality. "QCON", developed for the first time in Korea, is a technology that utilizes web/mobile to ensure quality and safety when pouring concrete. The concrete being poured on site can be monitored in real time via web/mobile, and the strength and defects of the concrete can be monitored by learning the historical concrete pouring data. QCON can analyze the 28-day estimated strength, actual strength, and various defect rates. Based on the above, information that warrants attention can be made available to the entire site to prevent defective products from being poured. In addition, QCON provides information such as the quality index that quantifies the quality level of each ready-mixed concrete supplier and the suitability of concrete pouring in consideration of current weather conditions to help obtain the highest quality concrete.
Hyundai E&C's Vision of True Concrete Utopia
Concrete technology has continued to evolve throughout its two thousand year history. Hyundai E&C, which is committed to concrete development more than anyone else, is also at the forefront of continued research and development to improve concrete quality. Concrete experts at Hyundai E&C will continue to lead the world beyond Korea, discovering new materials and converging technologies, mobilizing leading experts, and collaborating with global leaders to develop highly functional materials and innovate construction engineering technologies in a bid to realize its vision of concrete utopia.